発生頻度が低い不良が多項目にわたる場合、ひとつひとつの不良に対応するのは困難
こんなときは工程の生産性改善が品質改善につながります
不良率の低い不良がたくさん残っている
不良対策を実施する場合のセオリーはパレート図を書いて、寄与率の高い不良から対策するのがセオリーです
しかし、各項目の不良率が低くても、不良項目自体が多いとトータルとして不良率が高い場合があります
でも、不良率が低いたくさんの不良を順番に対応していくのは、時間もかかるし、効率が悪い
このような場合、生産性の改善が不良率の削減につながります
パレート図
不良対策をするときは:まずパレート図を作成して、重点を付けをするのが一般的です
下図のようなグラフが一般的なパレート図ですね
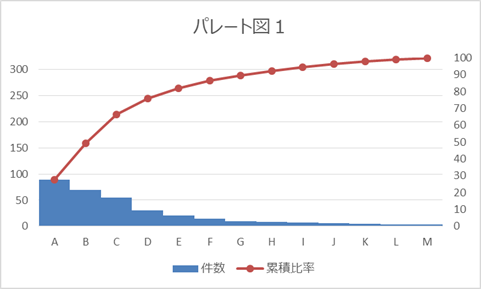
不良数の多いA、B、Cを優先的に対策打つと効果的に工場全体の工程不良を減らすことができます
これ、セオリーとして新入社員の時やQCサークルで勉強する内容です
しかしながら、主だった不良を対策完了したり、もともと不良の少ない工場は、同じ不良数でも下の「パレート図2」の様な分布になり、
不良数の多いA、B、Cの不良を対策しても、工程全体へ改善効果はそれほど多くありません
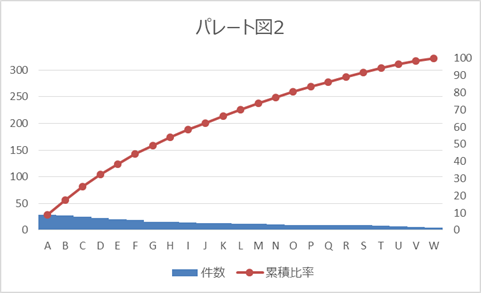
これを、不良項目ひとつひとつ対策していくと、かなりの時間が必要になるのがわかってもらえると思えます
こんな時に、どうするのが良いか
不良項目全体に効果がある活動が必要です
「そんな方法あるの???」
と思う人、いるかもです
私も、工場を担当し、色々考えてきたのですが、
一番良い方法は
工場の数多い慢性不良を下げる方法は「工場の生産性を上げる」
この結論に至りました
なぜ、生産性を上げれば不良が減るのか?
申し訳ないですが、論理的な説明はできません
私の経験則から生まれた感覚的な内容になりますが、工場の品質を良くするにはどうするか突き詰めていった結論です
生産性を上げる
まずは「生産性を上げる」意味から考えていきましょう
「生産性」とは、少し難しく言うと、
「限られた経営資源の中から、いかに効率的に付加価値を生み出すか」
となります
計算式で書くと
(付加価値)/(経営資源)
です
ただ、これは会社全体の生産性も含めて語る場合の考え方で、少しイメージしにくい人もいるかもしれません
今回は、工場の話ですので、それに合わせて「付加価値」「経営資源」を具体的なもののに置き換えます
工場の生産性を語る場合、よく使われるのが
分子(付加価値)を「生産台数」、分母(経営資源)を「人員×稼働時間」(工数)にした指標(KPI)です
生産台数/(人員×稼働時間)
一人当たり1時間でどれだけの台数を生産できるかを示します
また、分子を「粗利≒付加価値」にすれば
一人当たり1時間でどれだけの付加価値を生み出すことができるかを示しこともできます
さらに、分母を「人件費」または「人件費+設備償却費+工場経費」にすれば
工場費用当たりの生産性を示します
他にも、分子を台数ではなく生産額、さらには販売金額にする場合等、色々あります
これらの生産性を示す指標(KPI)は、工場の生産性を完全に示す指標ではありませんが、
それぞれの指標の特徴を知り使い分けるとにより、改善のポイントが見えてきます
私は現場改善活動で、現場のリーダーと話す場合は(生産台数)/(人員×稼働時間)を、
幹部と話するときは(生産金額)/(人員×稼働時間)を使ってました
リーダーに金額まで意識させるのは少し難しく感じましたし、幹部はやはりお金を意識してもらいたかったのが理由です
長々と書きましたが、結論
生産性を上げる=効率よく生産する
ここでは議論をわかりやすくするために「少ない人・時間で多くの生産する」
ことをベースに話をしたいと思います
生産性を上げるためのアプローチ
次に生産性を上げるための具体的な方法について話したいのですが、一つの記事では書ききれないので、
記事の主題の「生産性向上」=「品質向上」の理解が得られるように書きたいと思います
簡単に言うと、あらゆるムダをなくすことが生産性を良くすることにつながります
ムダとは「付加価値を生まない作業」です
工場での作業には次の4種類があります
- 加工
- 検査
- 運搬
- 停滞
1.加工
部品の組み立てや、材料を変形をさせて付加価値を生む作業
2.検査
付加価値は生みませんが、製品の品質を保証する上でしなければならない作業
3.運搬
これも付加価値を生まない作業。ゼロにはならないがなるべく小さくしたい
4.停滞
付加価値を生まず、全く必要のない作業。ゼロを目指す
つまり、
生産性の向上=ムダをなくす・減らす=「運搬」「停滞」作業をゼロに近づける
ことになります
「運搬」のムダを減らす
では、運搬の無駄にはどんなものがあるか考えてみましょう
ここでは、時間的なムダを考えてみましょう
・移動距離が長い
・積み替えが多い
・部品・材料を探す時間が長い
が、主な原因になります
これらのムダをなくすには
・大前提:在庫を最小化する
加えて
・前工程(サプライヤー含む)からの在庫置き場を近くする
・梱包を簡易にする
・在庫の定置・定量管理をする
等があります
在庫を最小化して上記のような対策を実施すると、運搬の無駄がなくなることは理解できると思います
(方法は今回は置いておきます)
さらに、移動、積み替え、部品探しで、時間のロス以外に、
部品・仕掛品に何らかのダメージを与える可能性を感じませんか?
これ、定量的に測ったり、実際の移動、積み替え、部品探しでダメージを与える現場を確認するのは困難です
ここが、ちょいと説得力に欠けてツライところではありますが
発生頻度が少ないから、測れないのが現実化と思います
しかし、ダメージを与える可能性が確実に高くなるとは考えられませんでしょうか?
私は、このダメージを与える可能性が不良率の低い多くの不良を作る可能性へつながると考えています
皆さんいかがでしょう
今一つ、論理的でないのが申し訳ないのですが、
数字的な実証を皆さんの現場で、例えば「在庫量と不良率の相関」を検証してみてはいかがでしょう
正しく計れば、きっと効果を確認できると思います
「停滞」のムダをへらす
次に停滞のムダについて話します
主な原因としては
・作業者の手待ち
・難しい作業
・部品切れ
・設備トラブル
等です
作業者の手待ちは、
流れ作業の中で、各工程のバラスが悪く、作業者Aは60秒かかるのに、作業者Bは40秒で終わる作業をしたら
作業者Bは20秒手待ちになります。
これムダです
また、組み立てにくい作業、取りにくい部品も作業者としては動いていますが、
付加価値を生まない無駄な作業になります
部品切れ、設備トラブルは言うまでもないですね
手待ちを無くし、難しい作業を無くし、部品が切れない仕組みを構築し、
設備が壊れないように保全活動をすることが停滞を無くします
ここで考えてみてください
これらのムダを発生させる原因が、不良につながる可能性いかがでしょうか
難しい作業はどうしても、組み立ての精度を下げます
組み立ての精度下げるとバラツキが増え、不良につながる可能性が増えます
バラツキと不良の関係はこの記事を参考に
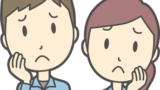
手待ちや、部品切れは作業のサイクリック性を失います
作業者は、決められた時間で、リズムよく、同じ作業を繰り返すこと(サイクリックな作業)により組み立ての精度を確保しやすくなります
さらに、設備トラブルは、その修理により、トラブル前と全く同じ状態に完全に戻せない可能性があります
その、全く同じでない状態が、組み立てのバラツキを大きくする可能性があります
では、このようなムダをどうやって減らすかは、また別の記事で話していきたいと思います
この、不良を生む可能性が「停滞」によって大きくなる可能性についてイメージしてもらえますでしょうか
「運搬」のところでも述べましたが、発生率の低い不良は頻度が低いために、その現場・現象を直接確認できる機会がなかなかありません
だから改善と成果確認に時間がかかります
ですので、その可能性を抑えるため、「停滞」無くしたいと考えます
まとめ
不良を発生させる可能性を下げるために生産性を上げること、工程のムダを無くすことを話しました
あくまで、不良発生の可能性の話で、ムダが必ず不良を作るわけではありません
ムダが不良を作る可能性が高くなる、これが0.01%高くなるだけかもしれませんし、全く不良とは関係ないかもしれません
でも、0.01%でも1万台生産すれば1台です
この不良をどう考えるかです
この記事の目的は、発生率は少ないけど、多くの不良項目を抱えている工程・工場全体の不良率を下げる方法を話しています
発生率の低い不良は、発生頻度が低いため、明確な原因を見つけるのは困難
よって、その原因と思われる部分の可能性を減らす活動が重要
そのためには、工程の生産性を上げることが工場として最も効果的と考えますが、皆さんいかがでしょう
コメント