現場の生産性の改善活動で、着目する要因が多すぎて優先順位を決めかねている担当者もいるかと思います。
そんな時、まず優先するべき項目として「在庫管理」から取り組んでみてはどうでしょう
在庫は工場の能力を測る指標です
「在庫は悪」とは良く言われます
確かにその通りですが、工場としての能力が低いのにむやみに在庫を減らしては工場の生産性の低下を招きます
工場の能力を高める活動により在庫を減らすことが重要です
工場の能力や生産性、在庫の関係を語ってみたいと思います
在庫は悪なのか
ネットとか本を見ると「在庫は悪」といろんなところで書かれています
経理からも、しょっちゅう「在庫を減らせ」と要求が来ます
なぜ悪なのか
・在庫を持つことで、資金が減る。資金調達が必要になれば金利負担がかかる
・在庫そのものは付加価値を生まない
・本来、売ることによりお金を得るものが、工場内に残っている=お金を稼げない
(材料購入、人件費用の現金は既に使っているのに入ってくるお金がない)
・長期保管による保管費用、さらには最悪、廃棄により損失
などなど、財務面でのリスクを言われます
まさにその通りで、基本的考えとして「在庫は悪」です
それは大前提です。誤解しないでください
ただ、単純に「在庫=悪」とは言えない面もあります
私は、「在庫は悪」とは言わず、
「在庫を適切に管理できていないことが悪」
と言うようにしています。
例えば、
「在庫が悪」なら「在庫ゼロ」がベストか?
決してそんなことはありません
在庫ゼロで、工場が適正に稼働しますか?
お客様に商品をタイムリーに届けれますか?
あの、世界のトヨタでもそんなことは無理です
この記事では「在庫を適切に管理する」ことで工程を改善することテーマに話します
「在庫を減らせ」では問題の解決にはならない
〇エピソード1
私が以前赴任した会社では、赴任当初、月末の在庫が極めて少なく、在庫目標を必ず達成する、一見素晴らしい会社でした
前任の社長は、調達、工程のメンバーを指導し、月末の資材(材料・部品)倉庫の在庫、工程内の仕掛在庫を徹底的に削減を実現していました
その結果どうなったか?
月初稼働初日に現場に行くと、作業者は座り込んで休んでいます
工程のリーダーに「なぜ生産しないの?」と聞くと、
「部品がないから」
すかさず
「なんで?」
「だって、月末に在庫を持ってはだめだから」
唖然 立ち尽くす私
毎月、稼働初日、生産用の部品が無く、ほとんど稼働しない状態が普通だと言うのです
ビックリです
この現実に全く疑問を持っていない社員たち
「社長の言うことは絶対」のカルチャーの中ではこうなるのか・・・・
毎月初日、倉庫の前には納品業者からのトラックが長蛇の列
やっと納品が終わって生産開始
しかし
工程の仕掛品もないので、各工程が一斉に動かない
前工程から徐々に生産が始まり、本体来にが動きだし、最初の商品が完成するのは、翌日・・・・・・
皆さん、この現実をどう思いますか?
果たして「在庫は悪」でしょうか?
上記の話は極端ですが、在庫が少ないために工程が止まることは良くあることです
何らかのアクシデントで部品が切れた時
(サプライヤーのアクシデント、前工程のアクシデント、調達のミス・・・色々です)
完成品の在庫が少ない場合は、お客様にタイムリーに納品できないですね
少なくとも、資材(部品)在庫・仕掛在庫を工場の能力以上に減らしすぎると、工場の生産性が低下しコストアップになることは理解できると思います
(この場合の「工場の能力」とは、受注、調達、計画、生産、出荷、品質、生産技術等すべての機能を含みます)
ここまでの話で、
在庫をむやみに減らすのも悪
ってことを理解してください
だからと言って、「在庫をたくさん持てばよい」わけではない
つまり、
「適正な在庫を持つ」 これが大事ってことです
適正な在庫とは
完成品の在庫まで考えると、話が複雑になるので、工程の生産性、品質に絞って在庫の意味を考えましょう
その場合、私の考える適切な在庫は
「「工程で部品切れを起こさない最小の在庫」
シンプルです
何じゃそれ!!
って思わないでください
確かに「在庫は悪」なのです
工程の生産性改善の面からみてもいっぱい理由があります
管理できていない在庫は、いろんなムダを生みます
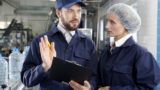
ですので、少ないに越したことはない
でも、少なすぎると工程が止まる
ではどうやって適正な在庫を決めるのか
結論を言うと、
適正な在庫=部品が切れない在庫=工場の能力によって決まる
と言うことになります
「部品が切れないための工場の能力]
と言うのは
・調達能力:タイムリーに部品をサプライヤーからの供給できる管理ができるのか
・設備管理:設備トラブルが発生しないような設備保守管理体制ができているのか
・社内工程間連携:後工程の生産計画に合わせて、前工程の生産計画が同期化できているか
等々
工場の能力と、在庫の量は相関があります
つまり、適正な在庫は工場全体の能力で決まります
能力のない工場が、無理やり在庫を減らすと、工程が止まります
〇調達の場合
少ない在庫で、部品を切らさないようにするには、
・工程の生産計画と納品計画が一致しなければなりません
・上記を1日レベルで一致させるのか、半日レベルか1時間なのか、はたまた1ケ月か、
それによって必要在庫量は変わります
時間が短くなればなるほど、難易度は上がりますが、在庫を少なくできます
・サプライヤが納品計画に合わせて確実に納品できる能力を持っているのか
設備トラブル、仕入れトラブルをしょっちゅう発生させて、納品遅れるようなサプライヤーでは、少ない在庫の場合耐えれないですね
「これはサプライヤーの問題だから知らん」と言っていても、生産が止まってロスするのは自分の会社です
〇設備管理
・設備トラブルが発生すると、在庫がない場合その後工程は全て止まります
・設備が止まっても、ロスを最小限にするだけの在庫が必要です
・設備の保守管理が十分できている工場は、そのリスクが低いため、少ない在庫でOKです
〇工程間連携
サプライヤーと同様、前工程も適切に部品を供給できず、且つ在庫が無ければ後工程は止まってしまいます
・前工程の生産計画と本工程の生産計画は同期できていますか
・同期できないなら、部品が切れないように在庫が必要です
・そして、同期ができる仕組みつくりをしなければなりません
トヨタはこれを「カンバン方式」という名のしくみで、作り上げています
トヨタも一朝一夕で作り上げたわけではないです
生産計画、生産能力、供給体制、設備トラブルの頻度等、
工場のいろんな要素を鑑みながら一歩一歩改善していくしかありません
これは、教科書にでいることではなく、各工場の状況、環境に応じてここで考える必要があります
言いたいのは
「能力のない工場にとって在庫を持つことは重要(管理できてることが前提)」
逆に言えば
「在庫を最小化するには、工場としての能力を高めることが前提」
「工場の能力を高めることが、在庫削減につながる」
となります
生産性を確保するために、沢山持っても良いのか
在庫を持つことの必要性を語りましたが、あくまで適正にかつ管理できてることが前提です
やっぱり在庫は悪なのです
これは忘れていけません
在庫をたくさん持つことによって、生産性の面から言えば
・たくさんの在庫から部品を探すムダ、積み替えるムダ
・在庫を管理する人・手間が必要なムダ
・回転率の低い(時には不移動)在庫がスペースを取って、必要な在庫を保管できないムダ
・在庫スペースがたらず、工程から離れたところに保管する、移動のムダ
・物量、移動増による、傷、変更等不良発生のムダ
があります
さらに費用面から
・不移動在庫発生による廃棄
・場所不足による、倉庫レンタルのムダ
・管理のために、人や設備導入のムダ
等々、資金・財務面だけでなく、工場をスムーズに運営するためには、やっぱり在庫は悪です
行きつ所
「適正な在庫を持つ」
「そして在庫を最小化できるように工場の能力を高める」
が結論です
まとめ
冒頭の、私が前に赴任していた工場の話
月末在庫を減らしすぎたために、月初の稼働が止まる
これも、結局
適正な在庫を見極めず、在庫を最小化するために工場の能力を高めることをせず、単に在庫を減らした結果です
いくら在庫が悪でも、適正な在庫でなければ、ムダ、ロスが発生することを中心に話しました
在庫を減らす活動=工場の能力を高める=工程改善=生産性向上
全てがつながっているということです
よって
在庫に着目して、工程改善することが最も効率的
と言うことになります
コメント