工場において工程不良は悩ましい問題の一つです
逆に言えば、工程不良を解決できれば生産性の向上、ロスコストの削減など経営的メリットも大きくなります
そして工程不良には2種類あります
(1)突発的不良
(2)慢性的不良
です
対策はそれぞれについて異なるアプローチが必要です
今回は(1)突発的不良について考えてみたいと思います
2種類の工程不良
上で述べた通り、工程不良には二つの種類があります
(1)突発的不良
(2)慢性的不良
の2種類です(あっさり😯)
はい、あっさり、この2種類です
それぞれ対策のアプローチが異なります
どちらも不良の発生の原因にアプローチしてすることには変わりありません
その問題の見つけ方が異なります
結論を言ってしまえば
(1)突発的不良=変化点を見つけその発生原因に対策する
(2)慢性的不良=仮説を立て試してみる。効果がなければ別の仮説を立てる。この繰り返し
今回は突発的不良についてです
突発的不良とは
まずは突発的不良
グラフで書いたらこんな感じ
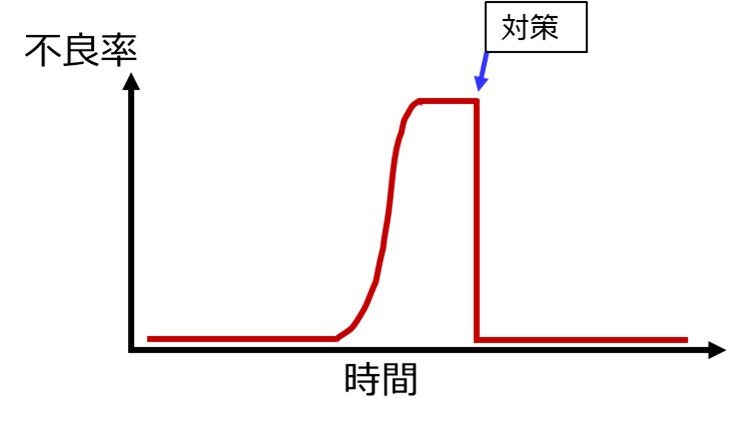
今までほとんど発生していなかった不良が突如発生
原因を見つけ対策後、元通りの低不良率に
このようなパターンです
このような場合の対策は
「変化点を見つける」
これにつきます
このパターンで、対応の報告を受けるときよくある話として
「治具の位置がずれて、部品を正しい位置に取り付けらてませんでした」
「部品の寸法がいつもより大きめに出ていました」
「作業者が間違った手順で組み立てていました」
みたいなパターンでしょうか
ちなみに、工程での品質保証の原則は
「正しい道具」「正しい部品」「正しい作業」
です
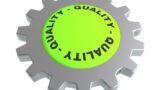
それぞれに問題が発生した事例を出してみました
一つ目の事例
正しくない道具「治具の位置がずれて、部品を正しい位置に取り付けらてませんでした」
この場合の変化点は「治具の位置」ですね
比較的わかりやすい
治具を正しい位置に戻して生産再開すればメデタシめでたし🥰です
イヤイヤ、
治具の位置がずれた原因がわかっていません
時間経過でねじが緩んだのか、😱
治具のメンテをしてた時、間違って取り付けたのか😵💫
変化点を作った原因もまた変化点です
しっかり追究しましょう
そうでないと、また発生します
正しくない部品「部品の寸法がいつもより大きめに出ていました」
これも比較的容易に直接的原因は見つけられます
「正しい部品に取り換えて対策しました!!😤」
イヤイヤ、やはりもう一レイヤー下げて分析しなければなりません
なぜ部品の寸法がいつもと違ったのか
部品製造時点で必ずどこかに変化点があります
金型?、作業者?、設備?、設備の条件変更?
それを見つけて変化点の発生原因に対策しないと再発可能性大です
あともう一つ
「いつもより寸法が大きい」
これも2種類の問題があります
・図面公差内の寸法でもいつもより異なる寸法だった
・図面公差から外れた寸法
それぞれ対応が異なります
ひとつ目、
公差内なら、「正しい部品」です
それでも完成品組み立て時に不良になることは設計が良くないことになります
(公差の設定は通常設計者が行います)
ですので、設計変更が必要です
設計変更の考え方はこの二つ
①図面の公差を、組み立て後良品になるレベルに設定する
②現状公差でも良品になるように設計変更する
どちらも大変です
①図面の公差を、組み立て後良品になるレベルに設定する場合は
部品製造の工程能力が問われます
今まで問題発生していないなら、今までの寸法になるように部品部門がしっかり管理すれば対応できるかもしれませんし、
今まで問題なかったのは偶然立ったかもしれません
現状の実力を検証して公差設定する必要があります
②現状公差でも良品になるように設計変更する場合
これは、チョイと難しい
製品の構造を見直さなければなりません
設計者に頑張ってもらいたいところです
もう一つの方法で、設計変更せずに製造側で対応する
寸法がばらついても正しい製品となるように、組み立て方法を考えることです
多くの場合、時間がなければこの方法がとられます
私も設計者の時、製造側に要求してました
しかし立場変われば言うことも変わる😎
「設計者は製造に負担をかける設計をするな!!」
と最近は言っております😱
もう一つの問題
図面公差から外れた寸法の場合、部品は不良品です(当たり前😁)
この場合、まずは不良が流出した原因を抑えなければなりません
検査が悪いのか、生産中に何か変化点があったのか
バラツキ(工程の力不足)なのか
この工程能力不足が厄介
対応は
・選別
・公差を許容できる設計変更
どっちも大変です
一番いいのは、バラツキを抑える製造の能力を高めることです。
ホントはこれば工場の現場力を高めることにつながるのですが・・・
現場の力が問われる場面です・・
正しくない作業「作業者が間違った手順で組み立てていました」
これは、新しい作業者を導入した時に発生することが多い問題ですね
現場で話を聞くとこの理由本当に多いです
変化点は「作業者」
これほどわかりやすい変化点はありません
でも、新しく入った作業者の作業の不適切が原因で不良を出します
「だからその変化点に対し事前に対策しようよ」
毎回繰り返される会話です
トレーニングや作業が安定するまでリーダーがつきっきりなるとか、
常にマルチスキルを身に着けるような人員配置をするとか
手段はありそうに思うのですが、現場でしかわからないできない理由があるのか?
ずーと悩んでいます・・・🤣
まとめ
工程で発生する不良の内、突発的不良の対策に対する考え方を書いてみました
現場で会話すると、「変化点に注目」なかなか浸透しないですね
地道に教え、職場のカルチャーになる領域なるまで頑張りましょう
後、もひとつだけ重要なこと
下の図の矢印⇔の期間
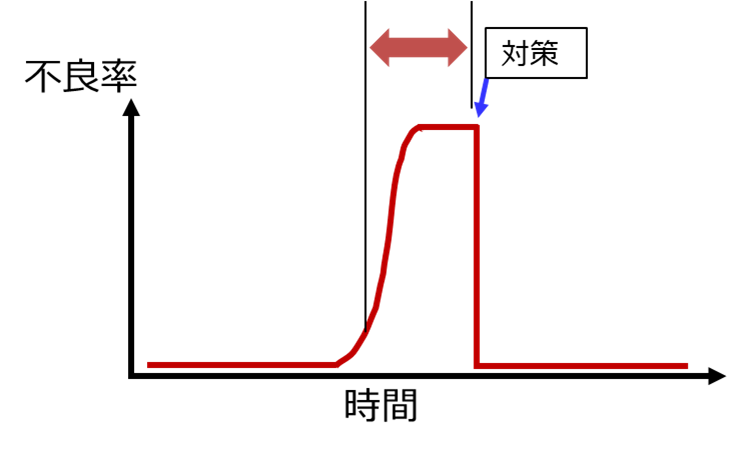
不良が発生し始めて対策までの期間です
この期間をいかに早く見つけて、対策を見つけるまで生産を停止
まず、異常と判断して早く生産を停止する
そして素早く対策する
停止までの不良数、対策までの時間
これも重要なKPIです
特に新しい作業者が入った場合、いきなり不良ゼロにできないかもしれませんが、
この期間を短くすることはできるはずです
現場責任者の人はぜひ、不良を出したことを叱る前に、この期間を最短にするように頑張った現場を評価してあげてください
コメント