ものづくりに関する記事を書いています
工程不良は工場において悩ましい問題の一つです
逆に言えば、工程不良を解決できれば生産性の向上、ロスコストの削減など経営的メリットも大きくなります
前回2回に分けて工程不良削減の考え方について記事を書きました
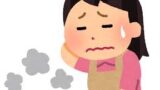
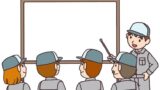
今回は工程不良の変化(良化・悪化)を確認した場合の管理者としての対応を考えてみます
工程不良が増えてしました!!
工程不良の数字が悪化したとき、
「工程で何か問題が起きている😱」
と考え、対策に動くことが普通の反応となかと思います
しかし、別の面からみると
「不良品の市場流出を止めることができた😯」
とも言えます
この点、皆さんいかがでしょうか
不良が増えた時は、まずはその不良を逃さず見つけた作業者、検査員をほめる
「よく不良を見つけてくれた、ありがとう😁」
この言葉をかけましょう
そうすることで、作業者・検査員の品質の意識が高まり、
「市場への不良流出防止」
という最もメーカーとして発生させてはならない問題を防ぐができる、という話です
その上で、不良を作らない対策を具体的に行っていきましょう
工程不良が減った!!
これも単純に喜んではいけません
何らかの意図をもって対策し、その効果との因果関係が明確な状態で工程不良が減った場合は素直に喜びましょう
しかし、因果関係がはっきりしない場合は要注意です
これ結構重要です
何も対策せず不良率が減ることは、普通はないと思ってデータを見るべきでしょう
こんな時、何が起こっているか
「不良の見落とし」です
原因は
・人的問題
・検査機の問題
・不適切な検査基準
の3つ
人的問題は
・検査員のミス
・検査員の変更によるスキル不足
等が考えられます
検査基準通りに作業ができているか、現場責任者は常に注意を払いましょう
加えて不良発生工程については、個別に指導しましょう
「〇〇不良が増えているから要注意」
と現場に指導しても不良は減りません
あくまで作業者一人ひとりに情報を聞いたうえで指導、もしくは作業方法の改善をしましょう
検査機の問題は
・検査機自体の異常
・条件設定のミス(これは人的ミスにになりますが・・)
になります
通常の工程では、1日数回、ダミー検査等で検査機が正常か確認を行います
それでも、稼働中に変化が起きたり、人的なミスをしてしまう場合もあります
不適切な検査基準は不良の見落としてしまう原因ではありますが、不良の減少の原因とは言いにくいですね
ただ、検査基準を変更する場合(=変化点)もあります
こんな時は超要注意です
結局、言いたいことは
「不良の削減=品質の良化とは言い切れない」
ということ
ぜひ、このことを忘れずに品質のデータを確認するようにしてください
まとめ
工程検査の目的は不良率を測定し工程の実力を測ることではなく、
「市場への不良の流出防止する」
であることをまずは認識しましょう
そうすれば、不良が見つかった場合は
「不良を見つけてくれてありがとう」
不良が減った時は
「検査に異常はないか」
という発想になるかと思います
いずれにしても、
データーに変化があるときは、現場にも必ず変化があります
その因果が明確な時は問題ありませんが、
「なんでだろ~」
と思うときは、良いデータ、悪いデータに関わらず「変化点」を確認すること忘れないでください
コメント