工場において工程不良は悩ましい問題の一つです
逆に言えば、工程不良を解決できれば生産性の向上、ロスコストの削減など経営的メリットも大きくなります
その工程不良には2種類あります
(1)突発的不良
(2)慢性的不良
対策はそれぞれについて異なるアプローチが必要です
前回は(1)突発的不良について話しました
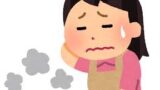
今回は(2)慢性的不良について考えてみたいと思います
2種類の工程不良
前回も述べた通り、工程不良には二つの種類があります
(1)突発的不良
(2)慢性的不良
の2種類です
それぞれ対策のアプローチが異なります
どちらも不良の発生の原因にアプローチしてすることには変わりありません
その問題の見つけ方が異なります
(1)突発的不良=変化点を見つけその発生原因に対策する
(2)慢性的不良=仮説を立て試してみる。効果がなければ別の仮説を立てる。この繰り返し
今回は慢性的不良についてです
突発的不良とは
慢性的不良をグラフで書いたらこんな感じ
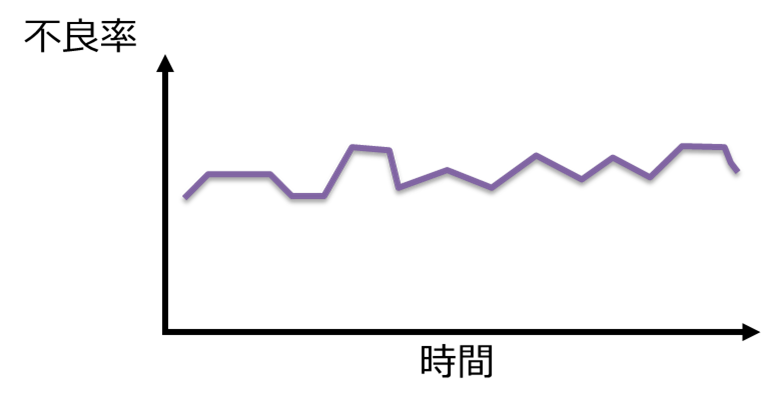
それなりの不良率で、ず~っと継続する不良です
参考までに突発的不良はこちら
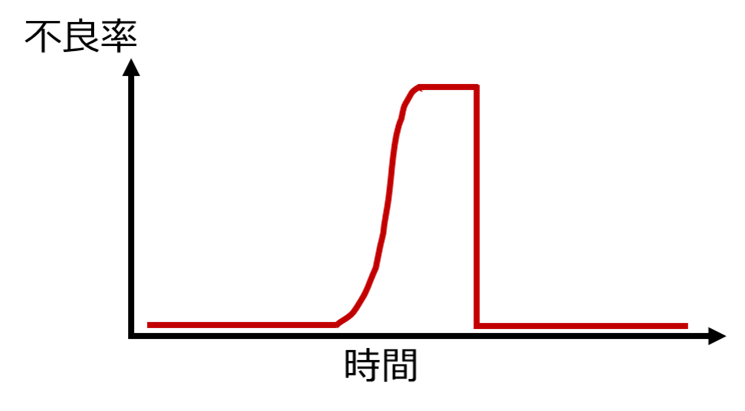
急に増えるタイプですね
今回のテーマである慢性的不良の原因を一言で言えば
「工程能力不足=バラツキ」
です😎
工場内のロスを生むだけでなく、このような不良はお客様にも継続的に流出する可能性が高く、
どの工場も頑張って対策するのですが結果がでなくて苦しみ、対策が遅れる傾向があります
多くの場合、
「なかなか効果的な対策を打てない⇒不良率が下がらない=バラツキを抑えられない⇒不良率を黙認しそのまま生産継続」🤣
状態ではないでしょうか
そんな厳しい状況ですが、対策として
「バラツキ発生の原因に対して仮説を立て対策を試す。失敗したら次の対策を考えて繰り替えす」
粘り強くこれを実行するしかないと考えています
・原因がわからず、原因に対する仮説を立てる場合
・原因は分かっているが、バラツキを抑える方法に対して仮説を立てる場合
二つの場合がありますが、どちらも仮説を立てる場合は
「正しい道具」「正しい部品」「正しい作業」
に注目です(突発的不良と同じです)
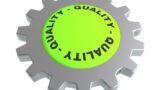
それと慢性不良の対策には、上記3つのポイント加えて
「正しい設計」
の観点が必要で、より重要になります
「正しい道具」で生産しているか?
この場合の道具と言えば、「治具」「金型」「機械・設備」等でしょうか
本来、これらは「バラツキを発生させない」=「同じものを量産する」ための道具なのですが、治具とかの設定が悪いためにバラツキが発生することも多々あります
固定が不安定とか、治具の少しの位置ずれが製品のには多く影響するとか
製品に対し治具を斜めにアプローチするときなどは、微妙な位置ずれが発生しやすいです
他にも金型の精度とか、設備が安定しないとか、
道具の精度を不安定にしているところがないか、よく観察し、悪い部分がどこか仮説を立て改善
そして結果を確認
一回のトライで改善することもありますが、多くはカット&トライが必要です
そして、結果が出れば標準化して品質の安定化を図ります
(QCストリーでいう「歯止め」ですね)
「標準化(歯止め)」は、他のアプローチで全て同じです
「正しい部品」が供給されているか
これは結局、部品製造部門もしくは部品サプライヤーのバラツキから発生するものですから、自社の製品へのアプローチと同じ考えを部品部門やサプライヤーで実施することになります
製品の品質部門や調達部門は常に部品部門、サプライヤーと連携を取って、バラツキを抑えることを要求することが必要です
しかし、多くの場合
部品が図面や仕様書通りに納入されているので、話がチョイとややこしい
当然、部品部門にしてみたら
「図面通りに作っとんのに何が悪いねん」
「仕様書通りに納品してるのに何が文句あるねん」
(少々ガラが悪いですが、私の若いころは・・・こんなオジサン、部品部門に多くて怖かったです🤣)
となります
つまり部品部門やサプライヤーにしたら「正しい部品」を納品していることになります
ほんで、公差を狭くすることを要求すると
「値段上がるけどええな」
となり、なかなか改善が進みません
こうなってくると、「正しい設計」これがポイントになってきます
後程詳しく書きますが、ある程度の部品のバラツキを許容できる製品設計が必要です
そうでなければコスト、不良率につながっていくことを理解しましょう
「正しい作業」ができているか
「正しい作業」=「作業標準書どおり作業」というのが基準になります
しかし、これも「正しい部品」と同様で、
「作業標準どおりの作業」をしても不良になる場合があります
これは、良品になる「正しい作業」を「作業標準書」に落とし込めていないことになります
また、作業標準書どおりに作業できない場合もあります
解決策としは、
不良が発生する作業を早く正確に見つける
「あたりまえやんけ・・」
となるのですが、これが意外に難しい
現場リーダーさんは現場の声を聞き、どこの作業のどの部分に不良の要因があるかを見つけなければなりません
ただ見ていても下がりません
(このポイントを見つけるの能力が工場の能力に繋がっていくと感じています)
データーの傾向を見ながら、どの工程の、誰の、どの作業に問題があるか
仮説を立て、改善を試みる
多くの場合一回のトライでうまくいきません
何回もトライ&エラーが必要になりますので根気よく対応していくことが重要です
そして
作業標準書を通りに作業をしても不良になるなら、バラツキが減るように作業標準書を変更します
これも仮説を立て、どのような手順で作業すればバラツキを抑えられるか何度も繰り返し検証して結果を出します
作業標準書通りに仕事ができていない場合は、作業者の問題か、作業標準書の問題かを見極めて修正しなければなりません
多くの場合、無理な作業を要求している場合が多いので、
治具化をするとか、工程設計を見直すとか、製品の設計の変更を開発部門に指示するとかアクションする必要があります
実際はもう少し丁寧なアプローチが必要ですが、詳細は別の機会に書きたいと思います
しかしながら、「正しい部品」の項でも述べたように、結局「製造しやすい設計」がベースになり、
このポイントを開発部門、設計部門が配慮した設計=「正しい設計」が重要になってきます
「正しい設計」がされているのか
公差に入っている「正しい部品」を使って生産し、作業者が「正しい作業」をしてもバラツキが抑えられず不良が発生する
こうなると、
設計の問題=「正しい設計」ができているのか
結局、この問題に行き着きます
設計部門・開発部門は
・ある程度のバラツキが許容できる設計
・組み立て易い・製造しやすい設計
これを達成する必要があります
これは、設計部門だけの責任ではなく
製造部門はそれを達成できるように開発の初期段階で情報を提供する義務があります
この情報提供をせず、開発最終段階、量産開始時に文句を言ってもできることは限られ、結局負担は製造部門が抱えることになります
また、不幸にも量産中でも問題を発見したら、製造部門だけで解決できない、困難とわかれば設計に情報を提供し一緒に解決してください
設計部門は、すでに次の新商品開発に追われていますので、なかなか協力してくれない場合が多いですが、よい関係を構築していきたいです
まとめ
2回に分けて工程不良の改善について考えてみました
(1)突発的不良=変化点に注目
(2)慢性的不良=仮説を立て改善⇒繰り返す
それぞれにおいてのアプローチの仕方を提言させていただきました
考えてみて、やはり工程の品質保証のベースは
「正しい道具」「正しい部品」「正しい作業」
であること、再認識した次第です
それと、慢性的不良は完全の効果が見れない場合どうしても現場は対策を後回しにしてしまう傾向がありません
しかし、そこは責任者、経営者が諦めたら終わりです
粘り強く現場を励まし、経営トップが注目していることを現場に意識してもらい、継続を促すことが大切です
経営トップが興味を持たない活動は、いずれ誰も推進しなくなります
皆さんの現場の改善に少しでもお役に立てれば嬉しく思います
コメント