製造業の現場において、製品の品質は企業の信頼や収益性に直結する重要な要素です
特に量産型の工場では、同じ作業が日々繰り返されるため、一度不良が発生すると、それが長期間にわたって見過ごされ、大きなロスにつながるリスクがあります
そのため、不良削減の考え方について記事をいくつか書いてきました
今回は、不良削減のための基本的な考え方として、
「不良発生ポイントの特定と対策」、「傾向の可視化」、「重点項目への直接コミュニケーション」
という3つのステップに焦点を当て、その有効性について書いてみみます
不良発生ポイントの特定と対策
不良を削減の第一歩は、「どこで」「どのような不良が」「なぜ」発生しているかを明確にすることです
つまりどこに「変化点」があるかを探すことが第一歩になります
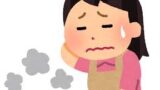
変化点の特定には、工程別・作業別・時間帯別などで分類することで、変化点の特定につながります
例えば、寸法不良が多発している工程がある場合、
・その作業のどの段階で寸法のズレが発生しているのか
・測定機器の問題なのか・
・作業者の手順にムラがあるのか
・環境の変化はないか
等を確認します。
傾向の可視化:グラフによる定量的な分析
不良の傾向を把握するためには、発生件数を定期的に集計・可視化することが不可欠です
以下のグラフは、3月から4月にかけての週次不良数を、不良項目別に積み上げ棒グラフとして表示したものです

このグラフのポイントは、時系列で不良の発生の変化を見ていることです
不良分析でよく「パレート図」が使われますが、私はあまりお勧めしません
理由は、時間経過が見れないからです
タテに、不良項目を積み上げた上記のようなグラフをおすすめしています
例えば、このグラフから以下のような傾向が読み取れます:
- 「寸法不良」が3月下旬から増加傾向にある。
- 「キズ」は全体的に減少しているが、一定数で推移。
- 「組立不良」は少数ながら継続的に発生。
グラフのように、週単位でデータを集計することで、
・特定の不良がいつから増えているのか
・改善策が効果を発揮しているか
といった点が可視化されます
さらに、グラフを部門ごと・ラインごとに分けることで、より細かい傾向分析が可能になります
この場合は、週次でなく日時で見ることも必要になってきます
(日時の場合はグラフではなく表形式の方がわかりやすいです)
これらの分析により、重点的に改善が必要な工程が浮き彫りになります
このグラフをもとにし毎週の改善会議で現場のリーダーが自ら不良データを説明することで、品質意識の向上にもつながります
不良発生工程の作業者と直接コミュケーションをとり問題点を抽出
可視化によって重点項目が判明したら、次にその不良が発生している工程を掘り下げて分析します
そして、最終的には
「その作業に関わる作業者」を特定し、ピンポイントでコミュニケーションを取り、作業の問題点を明確にし改善することが大切です
フォーカスするポイントは「正しい部品」「正しい道具」「正しい作業」です
つまり、作業者に対する指導・教育だけでなく作業しやすさや、部品のバラツキ、治具や測定器の不備など含めて確認します
- 準作業手順通りの作業ができているか
- 治具、計測器に不備はないか
- 部品のバラツキ、不良はでていないか
- 標準作業そのものに問題点はないか(不良を発生させやすい難しい作業はないか)
それらを見て、
作業を指導する、治具、計測器を是正する、部品精度を見直す、作業標準を見直す
等の対応をします
状況によっては「設計変更」を要求する必要があります
一連の流れで重要なのは作業者との直接コミュニケーションです
直接コミュニケーションはマニュアルだけではカバーしきれない現場の実情や、作業者のクセ・感覚的な部分にも働きかけることができます
また、作業者自身から改善のヒントが得られることもあり、現場力の向上にもつながります
実際に不良を頻発していた工程で、直接作業者とのコミュニケーションを行った結果、作業者から
「この手順はやりづらくて再現性が低かった」
「治具が使いにくく、不良にならないか気にしながら作業をしていた」
というようなフィードバックがあり、作業手順そのものを見直すきっかけになります
作業者自身からの発信はなかなか出てこないもです
現場リーダー、責任者自らからデータをもとに直接コミュニケーションを取っていきましょう
まとめ:現場とデータの両面からのアプローチ
不良削減のためには、「データによる傾向分析」と「現場への直接アプローチ」の両輪で取り組むことが重要性を紹介しました
今回紹介したグラフを活用した傾向分析と、そこから得られる気づきを作業者とのコミュニケーションと現場確認に落とし込むサイクルを回していくことで、継続的な品質向上が実現できます
品質の改善は一朝一夕ではありませんが、着実な現場改善の積み重ねが、やがて大きな成果につながります
現場の小さな気づきと、数字に基づいた分析を大切にし、組織全体で品質への意識を高めていきましょう
現場主導で進める不良削減活動は、単なる問題解決にとどまらず、社員一人ひとりの成長やチームワークの強化につながり、
「組織能力」が向上します
組織能力向上は、事業全体の戦略実行に繋がってます
これはまた別の機会に話することにしたいと思います
以前に書いた記事です
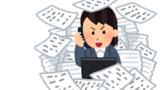
コメント