生産の異常をすぐに発見し、改善活動に結び付ける「生産管理ボード」について話します
「生産の状況が予定通り行われているか?」
を常に見える化し管理すことは工場経営の上で最も大切なことの一つです
そのために「生産管理ボード」が使われます
その目的は、生産の状況を知ることだけではありません
異常を把握しすぐ対応し、生産の遅れを最少化すること
現場の問題点を協会して全員で改善する
改善活動の効果を図ること
つまり、改善活動の重要な基本ツールになります
ボードに記入、入力することが目的になり、形骸化にならないようにしましょう
資産管理ボードとは
まずは、生産管理ボードについて
各社、いろんな情報を表示できるようにフォーマットを決めていますが、ここではオーソドックスな事例で
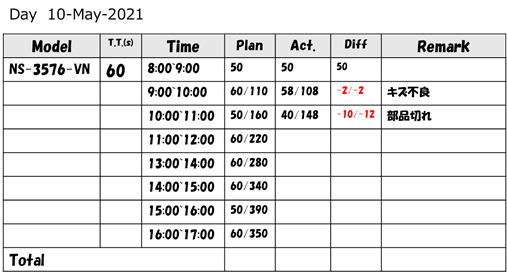
一言で言えば「予定通り生産ができているかを見える化するもの」です
最近は、こんな古典的なものではなく、IOTを導入して、いろんなダッシュボードで表示する会社が増えています
ただ、ITは道具であって、その情報をどう使うかが重要ですので、まずは、その情報を理解し、正しく使う、そして使うことを継続することが大前提になります。
ますは、生産管理ボードにどんな情報が必要か
・日付
・生産品目
・タクトタイム
必要な台数を生産するための、1台当たりの生産時間
例えば、1時間に60台生産する場合は60秒
・時刻毎の生産台数とその日の累計(計画及び実績)
例はマニュアルでの事例なので1時間毎になっていますが、
リアルタイムの表示する場合もありです
私は併用を勧めます
・計画と実績の差
・差の原因
言ってしまえば、そんな難しいものではありません
どこ会社でも普通に実施していると思います
ただ、この記事を読んで、本当に使えているのか、形骸化していないか、一度現場を確認してみてはいかがでしょうか
生産管理ボードの目的1
生産管理ボードの目的は
「生産状況の見える化」
が、1次的な目的になりますが、「見える化」は情報を得るための手段であり、本質の目的ではありません
一番の目的は、
生産の状況をリアルタイムで共有し、問題発生時の対応を行い、ロスを最少化する
になります
ですので、何か問題が発生したら、すぐに原因を分析し、対応を取ります
生産管理ボードの「Remark(備考)」には、遅れの原因を必ず書き込み、その情報を共有します
昔は管理ボードをラインの横に設置していましたが今はIT技術を使って、すぐに事務所とも情報を共有できるようになりました。
このように、生産の状況を常に管理できる状況を取り、トラブルを放置することをせず対応し、生産の遅延を最少化し、お客様に確実に商品を届ける
工場としての最も重要な役割を果たすための、基本ツールであります
生産管理ボードの目的2
も一つの目的、問題を見つけるための重要なツールになります
改善するべき問題点を見える化する
現場は改善するべき問題を常に持っています
それを見えるかし、全員でレビューして改善活動に結びつけています
トヨタ生産方式では「大部屋」活動と呼んで、毎日問題点を共有して、積極的に問題を解決することに手を挙げて改善していきます
そのとき、生産管理ーボードに書いている問題が改善のベースになります
トラブルでも、その場で処置すれば済む問題もありますが、少し時間かかる、周りの協力が必要な問題もあります
そのような問題を解決することが改善に結びついていきます
生産管理ボードの目的3
改善活動が狙い通りにできているかを見るために、常に管理する
するために使います
生産性を上げるために、生産数を維持しながらタクトタイム減や人員減を目指すことは一般的にどの工場でも行っていいます
その活動が狙い通りにできているか、
管理ボードで常に確認し、狙い通りにできていない場合はすぐに活動の見直しが必要です
作業時間を計測してもタクトタイムをオーバーすることはない
部品・品質、機械のトラブルもない
しかし少しづつ、生産台数が計画より遅れる
みたいなことは、多々あります
各工程の作業時間を減らしたつもりでも、実は設備の稼働が追い付かず、そこがボトルネックだった
作業自体には問題なないのに、
部品の供給の仕組みに問題があり、部品切れによる小さな作業停止が発生してて、作業者自ら部品を取りに行ったりしていることが往々にしてあります
また、作業のバラツキが大きく、作業時間の計測時には安定した作業だったのが、実は、かなり時間がかかるときがある
(部品のバラツキで勘合しにくい、リード線が絡みつく 等の作業でありがちです
このような場合、改善して作業時間を縮めたつもりでも効果がなく、最終アウトプット(完成品台数)を見なければわかりません
改善のアウトプットは、最終の生産台数で測ることが重要ですね
それが、工場のアウトプットそのもですから
(参考)標準工数について
コスト計算をする場合等に「標準工数」(組み立てに要する総時間)を使用するケースがあります
注意しなければならないのは、標準工数を減らしても、生産性がよくなるとは限りません
いくつかの作業を並べて連続的に組み立てるライン作業で生産をする場合、
工程の中にボトルネック作業があれば、その作業により生産能力が決まるからです
これも、アウトプットを見ていれば改善できていないことがよくわかります。
資産管理ボード使用時の注意点
生産管理ボードを目的通りに使用すれば何の問題もないのですが、
なかなか、そうはいかないケースもよくあります
形骸化している場合ですね
立派なシステム入れても、その得た情報を生かすことができなければ意味がありません
見える化をすることにより、見えた情報を生かし改善する責任が発生する
ことを忘れてはいけません
「見える化」や「IT化」はあくまで手段であって目的ではないってことです
在庫が多い時も同じですが、生産管理ボードを見なくてもとりあえず生産はできます
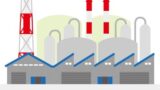
部品の納品が止まったり、設備が壊れたりした場合は影響が大きく、皆が注目しますが
工程で起きる小さなトラブルは、少々生産が遅れても、残業等でごまかして、発生防止を活動をしない場合が多々あります
そして、「なせ残業するのか? 生産が遅れているのか」と聞くと、部品切れや、設備トラブル等の大きな問題だけを取り上げ、日常の細かなロスを放っておきます
確かに大きな問題から手を付けることは重要ですが、果たしてそれでいいのか?
結局、
小さいロスを見逃す、放置する体質はロスに対する不感症になり、
大きい問題を誘発する体質につながっていきます
皆さんいかがですか?
まとめ
生産管理ボードについて説明しました
生産活動の最もベースとなる情報を提供するツールです
しかし、形骸化になりがちなツールでもあります
このような基本を軽視する体質は、ロスを発生させることに対する感度が鈍くなり、だんだん大きなロスに対してまで感度が下がります
一度、現場の生産管理ボードの活用状況見てみることお勧めします
コメント